If the process can be modeled as a constant model, new developments in metal cutting technology can produce the greatest economic benefits. From the perspective of comprehensive or global production economy, this is extremely important for comparing different feasible technical solutions. The definition of global production economy is: “Ensure maximum safety and predictability of the process while maintaining maximum productivity and lowest production costs.†Before a detailed 1:1 optimization of a single process, it must be viewed from a macro perspective. Balance and optimize the overall picture of process productivity and cost effectiveness. After taking this step, you can achieve further improvements by carefully investigating situations that are suitable for 1:1 optimization.
Microscopic and macroscopic models
To achieve optimal metal cutting results, the traditional approach uses a narrowly defined microscopic model based on a 1:1 optimization of a single tool in a single pass. On the other hand, the macro model considers manufacturing in a broad sense. In these macro or global models, the total time required to produce a particular workpiece has a more decisive role.
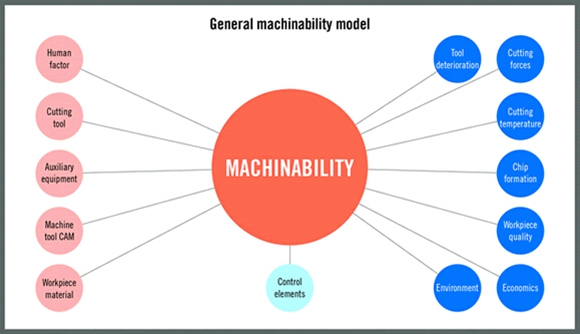
A simple example of global optimization is the production of components using two machine tools in a production line. If the same improvement can be made to machine "B", the cutting time optimization and production increase for machine "A" is useless. The increased production of machine "A" will only result in an increase in the inventory of semi-finished workpieces waiting to be machined on machine "B", resulting in additional costs. In this case, it is better to optimize the cutting cost on machine A. Doing so may limit the productivity of machine A, but it will reduce the total cost while maintaining production.
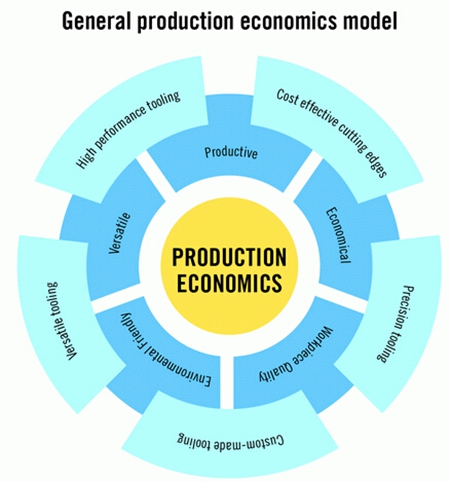
On the other hand, when machine B waits to machine the parts produced by machine tool A, increasing the output of machine tool A will increase the total output. This depends to a large extent on how the shop organizes its production and processing: whether it is processed in production lines, processed in batches, or processed in parallel. Although it is not possible to generalize the various situations, these examples all show that it needs to be a global perspective, and it also shows that micro-model optimization needs to be carried out very carefully.
The requirements from a global perspective can be applied to the machine itself. Typically, a workshop can run a milling machine at full load 40 hours a week, and it decides to replace it with a high-speed machine. When the new machine started to operate, it was idle for half of the time. This puts the shop in the face of the challenge of finding new jobs to keep the new machine running, so there is an additional cost to prove the rationality of the investment. A better approach is to first look at the overall situation and estimate what happens to the larger production of the new machine.
Optimize cutting time and cutting costs
The 1:1 optimization focuses on an application and a single tool designed to produce high metal removal rates at the lowest possible cost. The process involves selecting the tool that is most suitable for the machined part and using the maximum possible depth of cut and the highest feed rate. Of course, the maximum depth of cut and feed rate are affected by machine power and torque, workpiece clamping stability and tool clamping safety.
The final step in the 1:1 optimization is to select the appropriate standard for the lowest cost or maximum productivity and use the cutting speed to further optimize the implementation of the standard. It is important to remember the Taylor model used to determine tool life. This model demonstrates that for a given combination of depth of cut and feed, there is an optimum range of cutting speeds where tool losses are still safe, predictable and controllable. When working in this range, it is possible to characterize and quantify the relationship between cutting speed, tool wear and tool life.
Initially, as the cutting speed increases, the processing time decreases and the productivity increases. But after increasing to a certain speed, the cost starts to rise again. After a certain cutting speed is exceeded, the tool life begins to shorten, so that the cutting edge needs to be replaced frequently. From a global perspective, the impact of reduced processing time costs is less than the impact of rapid tool cost increases. Therefore, the tool has a cutting speed that allows the sum of the two costs to be balanced to achieve the lowest total cost.
In the pursuit of productivity, the shop must be cautious, do not pay too much attention to the production details and not fully consider the overall, that is, the total process time used to produce the workpiece.
Quality and productivity: sufficient but not redundant
Today, people's requirements for the quality of parts are more stringent than in the past. However, achieving the highest levels of quality can sometimes seem overwhelming. High quality is good, but too high quality wastes money. The simple theoretical problem summarizing this situation is: “How do we produce the worst-case workpieces with acceptable functions?†By only meeting this minimum requirement, the cost can be greatly reduced and the productivity can be significantly improved.
Similarly, if you only focus on achieving the highest productivity in a short period of time, the reliability of the metalworking process will be reduced. When continuous processing is performed under low feasibility and the limit is exceeded, the cost is that the workpiece is unqualified or scrapped and lost time.
Quality, production time and cost
Productivity includes three factors: quality, production time, and cost. In addition, environmental factors such as energy consumption, disposal or recycling of worn tools, waste disposal, and safety factors related to employee health must be considered.
Many individual technical factors can affect production efficiency. For metal cutting processes, there are 50 - 70 individual factors that affect efficiency, and often one or more factors can have a significant impact on efficiency. Typical factors include tool/tool ​​system, workpiece configuration and materials, equipment processing capabilities and parameters, human factors, external equipment, and maintenance issues.
One of the biggest influencing factors is the result of the interaction between the tool and the workpiece. Understanding tool wear and failure modes is critical to controlling metal cutting processes. Signs of wear are usually gradual and predictable, while other failure modes, such as tool breakage, lack the necessary predictability and therefore cannot maintain a reliable cutting process.
Universal tool
For balanced productivity, reliability and tooling costs, tools that offer versatility and flexibility in a wide range of applications are required. In addition, the multi-purpose or general-purpose tool (see sidebar below) also satisfies the tendency of the manufacturing industry to develop significantly into smaller batches. The shift to smaller processing volumes stems from an increasing use of just-in-time production strategies and increased outsourcing.
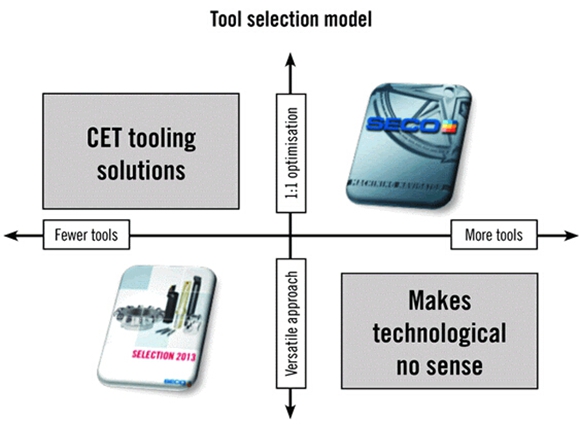
Currently, subcontractors require regular, but not continuous, production of small batches of workpieces. In the past, the automatic tool changer helped to reduce the downtime caused by tool change, and with the use of the fixture changer, the downtime caused by workpiece handling was reduced. Universal tools reduce the time required to load new tools during workpiece change and eliminate the need to set up and test new tools, thus reducing downtime. In addition, due to the reduced number of different tools in the shop, the tool processing time is also reduced and the machining operation time is increased.
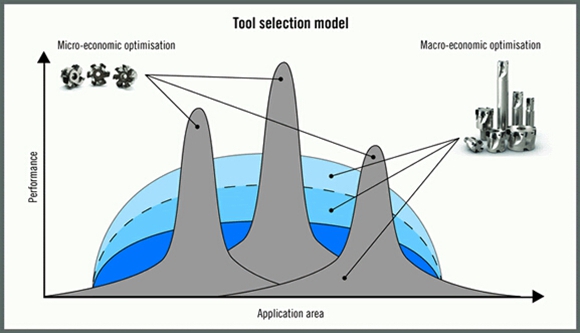
Traditional tool selection strategies tend to be based on applications: for example, tools for steel, stainless steel, or tools for roughing or milling applications. More important than choosing a tool for a single process is how to make the process meet global requirements. This choice should tend to which tool is needed from a productivity, cost-effective or reliability perspective, and which tool is best suited to the entire production process.
Simple solution
Process optimization from a global perspective is not necessarily complicated, it can take some very basic and simple operations and analysis. Testing an used tool is an important example. A correct understanding of the situation presented by the tool provides a comprehensive understanding of the work carried out in the workshop. For example, if the shop is generally a blade with a cutting edge of 12 mm and the wear on the tool is only 2 mm or 2.5 mm, the blade used in the shop may be too large for the work performed. It is more than enough to use a tool with a cutting edge of 6 mm, and a tool with a cutting edge of 6 mm is much cheaper than a tool with a cutting edge of 10 mm. This simple observation reduces tooling costs by 50% without reducing productivity.
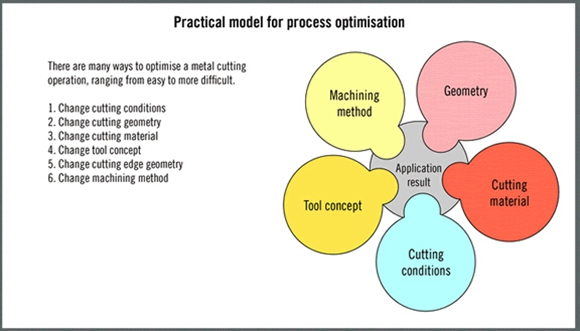
Tool manufacturer's response
Today, toolmakers recognize that customers are increasingly eager to respond to high-productivity and cost-effective general-purpose tooling systems. Newly developed universal tools increase tooling while reducing tool inventory, tool handling, re-tooling and testing costs.
An example of such a tool is Seco's Turbo milling cutter series. These tools offer exceptional versatility and flexibility in a wide range of applications, delivering outstanding cost and performance. They are designed to provide error-free production and high quality workpiece surface roughness. These tools feature a positive cutting geometry that reduces power consumption, extends tool life and maximizes depth of cut and feed rate. The ability of these tools represents the first step towards an overall optimized process.
Another way to use a universal tool is to assemble a set of tools for a variety of applications. Seco's selection of tools is designed to provide flexibility. The selected tool set includes a limited number of tools that may not necessarily provide absolute maximum productivity or cost effectiveness, but they are the most economical and best for processing the ever-changing variety of workpieces and components required for maximum flexibility. select.
In essence, this approach is not suitable for a variety of needs. For example, in contrast to highly specialized products, such as PCBN tools, they are designed for extremely high quality and/or extremely high productivity machining of specific workpiece materials. PCBN tools are very expensive, but they are the best choice for some professional applications.
From another aspect of the batch, custom engineered tools (CET) is a method tailored for high volume production of specific applications. The tool is designed to limit the inventory requirements for different tools, but it is still possible to achieve micro and macro optimization.
Just as manufacturing plants must choose metal cutting technology from a global perspective of the entire production process, tool manufacturers must develop product lines that meet a wide range of customer needs.
Headquartered in Fagersta, Sweden, Seco is committed to developing innovative metal cutting solutions and working closely with customers to fully understand and focus on meeting their needs. We employ more than 5,000 people in 50 countries and enhance the capabilities of our team members through training, development and employee recognition programs, and an open communication environment. Our employees demonstrate three core values ​​– enthusiasm, family belonging and personal commitment – ​​which define the way we do business and how we interact with our customers, suppliers and other partners. For more information, please visit
Samarium Cobalt (SmCo), as the second generation of rare earth permanent magnets, not only has a high magnetic energy product (14-32mgoe), but also has a reliable force, and has a good temperature characteristic in rare earth permanent magnet series.Samarium cobalt is more suitable for working in a high temperature environment than Ndfeb Magnets.
Samarium Cobalt
Samarium Cobalt,Samarium Cobalt Magnet,Samarium Magnets,Smco Permanent Magnets
Chongqing Great Well Magnet Co.,ltd. , https://www.gwmagnet.com