Planetary wheels are important parts in wind turbine gearboxes. Planetary gearboxes are the most prone to failing primary gears in wind turbine gearboxes. Therefore, planetary gears are required to have sufficient strength, rigidity and toughness. Hardened surfaces and tough cores will be better. Wear resistance and high impact toughness. The gearbox is designed to achieve minimum mechanical noise, but the gearbox noise will increase due to tooth surface wear. Increasing the surface hardness and wear resistance will reduce the gearbox noise. In this regard, the carburized gear has a hard tooth surface and toughness. It is an advantage for reducing noise.
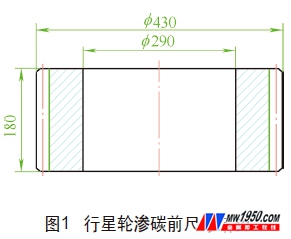
When low fatigue life and high toughness are required, ordinary low alloy steel is not suitable as carburizing, and high performance nickel chrome molybdenum steel can provide deeper hardenability and high fatigue strength. At present, 18CrNiMo7-6 has become the mainstream standard gear steel for wind turbine gearboxes. 0.15%~0.5% molybdenum element is added into carburized steel to improve the hardenability of the low carbon zone and the toughness of the surface high carbon zone. Wind power gear parts are particularly significant.
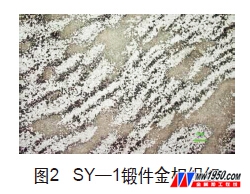
First, the test product
In order to achieve comparative analysis, two identical smelting furnace numbers were selected, and the wind power planetary gears with different metallurgical uniformity levels of different forging processes were subjected to carburizing quenching and tempering test. After forging heat treatment, isothermal normalizing process was used to obtain pearlite and ferrite. Body balance organization. The metallographic structure of the SY-1 test piece was grade 6 and severely uneven; the metallographic structure of the SY-2 test piece was level 2, relatively uniform. The structural dimensions of the planetary wheel before carburizing are shown in Figure 1. The test piece information is shown in Table 1. The chemical composition of the body is shown in Table 2. Figure 2 and Figure 3 show the metallographic structure of the planetary wheel body forging.
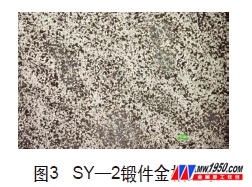
Second, the test equipment
The carburizing and quenching and tempering heat treatment is carried out by the well type carburizing furnace and the martensite grade quenching production line. The quenching medium with a certain water content of 50% KNO3+50% NaNO2 is used to improve the high temperature cooling rate of the quenching cooling medium, so that the planetary gears are excellent. The heart organization, improve the toughness.
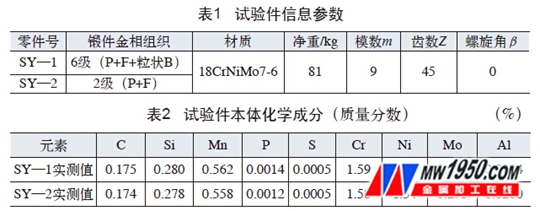
Carburizing and quenching heat treatment process: carburizing furnace carburizing → slow cooling to room temperature after carburizing → reheating austenitization → salt bath quenching → air cooling typhoon cooling → cleaning nitrate salt → low temperature tempering. Martensitic graded quenching line (see Figure 4). The comparison of cooling parameters of 50% KNO3+50% NaNO2 nitrate salt medium is shown in Table 3. The technical parameters of the main heat treatment production equipment are shown in Table 4.
Third, carburizing and quenching process
The two test pieces are heat treated by carburizing, quenching and tempering, and the process curve is shown in Fig. 5.
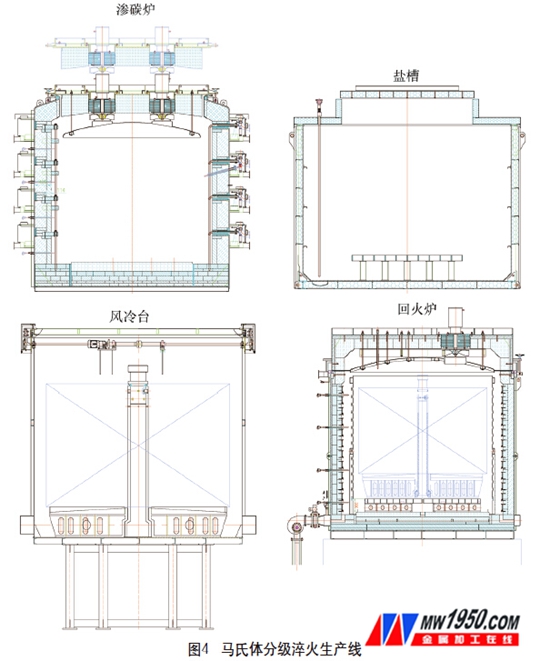
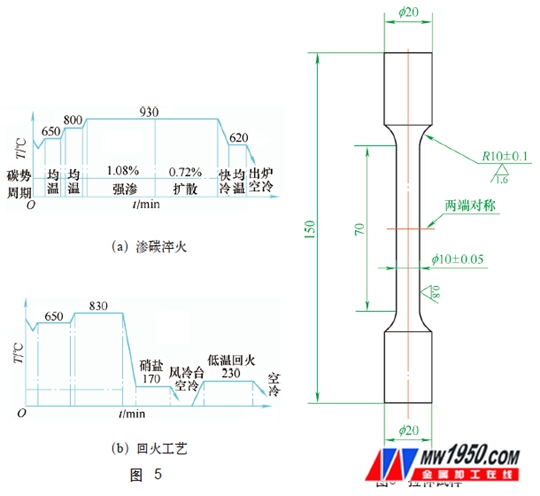
Fourth, test results and analysis
After carburizing, quenching and tempering, the mechanical properties of the two test pieces were tested. Each piece of wire was cut and cut into 4 sets of core longitudinal and three pull blanks. The tensile impact test samples are shown in Figure 6 and Figure 7. The anatomical position is shown in Fig. 8. The distribution of the shock absorption energy scatter is shown in Fig. 9 and Fig. 10, respectively. The mechanical test results are summarized in Table 5 and Table 6.
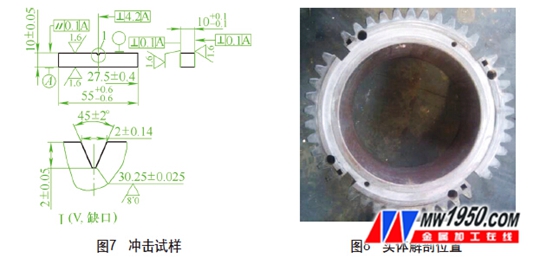
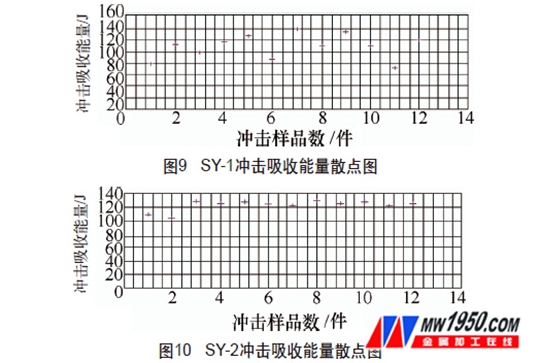
Test result
(1) Strength analysis The tensile strength SY-1 average value is 1195 MPa, the tensile strength is extremely poor at 40 MPa, the SY-2 average value is 1213.75 MPa, and the tensile strength is extremely poor at 10 MPa. Yield strength: SY-1 average is 1020MPa, yield strength is 50MPa; SY-2 is 1057.5MPa, yield strength is 20MPa; SY-2 strength is slightly higher than SY-1. The reason why the intensity of SY-2 is slightly higher is that the hardness of the SY-2 core is slightly higher than that of SY-1, and the tensile strength is proportional to the hardness. The strength test results show that the uniform and small forged microstructure is beneficial to improve the carburizing and quenching hardness, strength index and strength uniformity test piece strength scatter distribution, as shown in Figure 11.
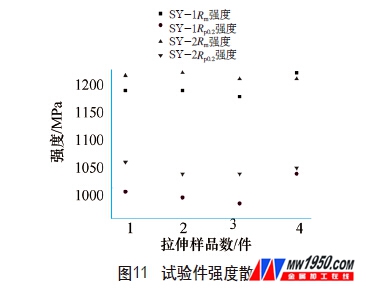
(2) The average elongation after fracture S Y-1 is 10.625%, and the average value of SY-2 is 10.375%. Shrinkage rate: SY-1 average value is 49.875%, S Y-2 average value is 49.375%, SY-1 plasticity index has no significant difference with SY-2, slightly higher reason is that strength is inversely proportional to plasticity, SY-1 intensity The value is slightly lower than SY-2.
(3) The average value of the shock absorption energy S Y-1 is 9 8 . 4 2 J ; the average value of S Y- 2 is 122.8J; the dispersion of the three impact values ​​of each group of SY-1 is large, and the impact energy of the four groups is extremely poor. It is 31/40/28/48(J); S Y-2 impact performance is relatively stable, and the impact energy absorption of the four groups is 25/3.0/8.0/6.0 (J). The test results show that the uniform and small forging microstructure is beneficial to improve the toughness index and toughness uniformity after carburizing and quenching.
(4) Hardness The hardness of the two planetary cores meets the technical requirements of 35~45HRC, but the deviation of SY-1 single piece is 5HRC, and the deviation of SY-2 single piece is 2HRC, indicating that the uniformity of the structure is worse, the more the hardness deviation of the core of a single piece is Big.
The mechanical test results show that the mechanical properties of the body are as shown in Table 6. The mechanical properties of the SY-1 and SY-2 sections are in accordance with the requirements. The circumferential distribution of the mechanical properties of the SY-2 test piece is relative to SY-. 1 is more uniform, indicating that the metallurgical structure of the forging metal grade 6 causes the mechanical properties to fluctuate, especially the toughness, and the metallographic structure uniformity 6 has a far greater negative impact on the toughness than the metallographic uniformity.
The test results show that the uniform and fine forging metallographic structure can improve the strength and toughness after carburizing, quenching and tempering. The metallographic structure unevenness has a greater negative impact on the toughness than the core hardness, tensile strength, yield strength and elongation. The negative effects of long rate and reduction of area. Although the mechanical properties of the SY-1 test piece can still meet the corresponding technical requirements, the performance stability is reduced, the planetary wheel mechanical design margin is reduced, the planetary gear failure will be initiated in the weakest area of ​​performance, and the planetary wheel is caused by the large dispersion of impact toughness. The probability of failure will increase.
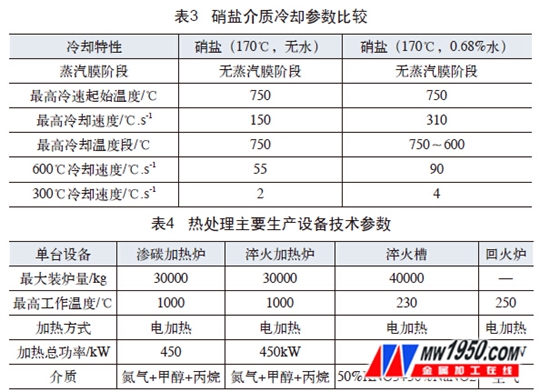
2. Test analysis
The main reason for the occurrence of non-equilibrium granular bainite is the uneven distribution of chemical composition and stress field. During high-temperature austenitization, the content of alloying elements in austenite will be unevenly distributed, which tends to grow grain. Different, easy to obtain mixed crystal structure. Segregation occurs when the ingot solidifies, resulting in non-uniformity of composition and structure. Therefore, the original steel ingot must have a certain degree of dendrite segregation, especially 18CrNiMo7-6 low-carbon alloy structural steel. The ingot is more likely to cause severe dendrite segregation. .
The internal structure of the ingot is mostly uneven dendrite structure, the grain is coarse, and there are defects such as pores, shrinkage holes, non-metallic inclusions, etc., but the deformation is deep into the inside of the steel ingot through forging and flexible forging, and its organization will be Great changes have occurred, the original coarse tissue will be improved, and the pores, shrinkage cavities, etc. will be forged together, fully destroying the as-cast as-cast structure, the various segregation zones are improved, the composition is further homogenized, and the structure is more compact. The uneven dendritic structure inside the steel ingot has high stability and cannot be eliminated by conventional heat treatment. It can only change the uneven distribution of the original structure by alternately thickening and lengthening in different directions. If the forging process is unreasonable The as-cast structure is not fully broken and homogenized, and uneven grain and tissue distribution patterns will be obtained after forging, which will cause long-lasting and fatigue performance degradation.
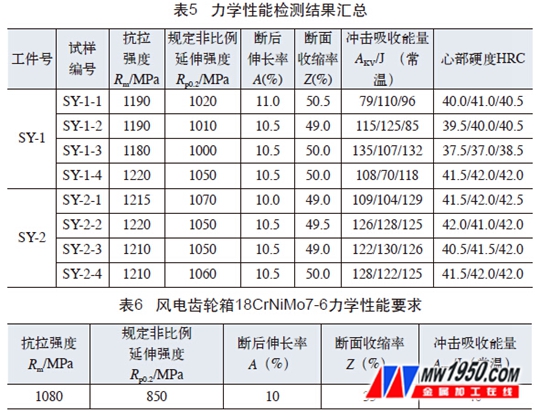
The metallurgical structure of the uniform planetary gear after final carburizing, quenching and tempering, the room temperature mechanical properties are uniform and excellent, usually uniform and fine grain structure can improve the strength and toughness of the material, because the more uniform and fine grains, the more grains of different orientation, The greater the dislocation motion resistance, the higher the strength and toughness. The original microstructure of the forgings is uneven, indicating that there are differences in the composition of the micro-regions, which will inevitably lead to differences in the hardenability of the micro-zones. The morphology and distribution of lath martensite in the mechanical samples after carburizing and quenching will be uneven, due to the mechanical properties of toughness and other mechanical properties. The organization decided that the uneven quenching structure will lead to the discrete distribution of mechanical properties such as toughness. The greater the unevenness of the original microstructure of the forging, the more serious the dispersion of mechanical properties such as toughness. Under the impact load, due to the large loading speed, the plastic deformation is not fully developed. Therefore, the test of the notched impact specimen under the impact load can reflect the tendency of the material to become brittle, and can sensitively show the internal structural defects and the microstructure changes. The effect of the static load tensile test method is relatively low.
V. Conclusion
(1) The metallographic structure of uniform and small forgings can improve the strength and toughness after carburizing, quenching and tempering.
(2) The uniformity of metallographic structure significantly affects the toughness index. The worse the uniformity of the structure, the worse the uniformity of toughness.
(3) The negative impact of metallographic heterogeneity on the toughness index is greater than the negative impact on core hardness, tensile strength, yield strength, elongation after fracture and reduction of area.
(4) For wind turbine planetary gears, the metallographic structure of the forgings is uneven, so that the impact toughness is discretely distributed, the safety factor is reduced, and the failure probability is increased.
About the author: Gu Xiaoming, Jiang Weijie, Changzhou Tianshan Heavy Industry Machinery Co., Ltd.
Cooking is a lot more colorful when you use Silicone Spoon. Great for mixing, stirring, sautéing or serving, the silicone material won't scratch non-stick pans or bakeware and withstands heat up to 350 degrees.
All-purpose spoon can be used for cooking, baking and serving
Silicone Spoon,Silicone Spoon Baby,Silicone Spoon Mold,Small Silicone Spoon
BOHAO ENTERPRISE CO., LTD , https://www.yj-bohao.com