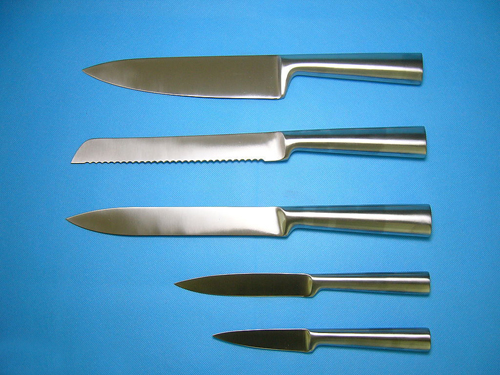
(1) The momentum of rapid development is unstoppable. Although there is macro-control, it is still in a stage of continuous development.
(2) "Speed, accuracy, efficiency, and environmental protection" have become industry consensus.
(3) The competition is fierce. State-owned enterprises restructured and restructured, foreign-funded enterprises settled in one after another, and private enterprises emerged with the survival of the fittest. In view of the above-mentioned severe situation, the domestic tool industry should review the situation, take the market as the guide, actively adjust the industrial structure, improve product quality, and develop new tools that are suitable for people's livelihoods such as automobiles, high-speed rails, and home appliances. Looking at the hot industries such as machinery, molds, and energy in recent years, the tool market in China is very promising. Nowadays, China has become a major machine-building country in the world. In the future, the world’s tool market will be in China. Occupying the Chinese market will occupy the international market. Change the concept Accelerate the development of the change in the concept of cutting includes two aspects: the concept of thinking and the concept of production and management.
(1) Thinking concept How to improve efficiency and reduce costs? In the past 20 years, the cutting speed has increased by 5 to 10 times, but the machining efficiency has only increased by 50% to 100%. One of the reasons is that the effect of improving the cutting efficiency is occupied by a large amount of non-cutting time. In recent years, China's cutting machine tools have developed rapidly. The number of possessions is far ahead in the world and ranks first, but the tool industry is lagging far behind. As the saying goes, a good horse is equipped with a good saddle. If advanced machine tools are not matched with advanced tools, efficient machining efficiency will not be realized, which will seriously affect the improvement of production efficiency and restrict the development of manufacturing to modernization. The concept of heavy-duty, light-weight tools has been deeply ingrained in many people's minds, and the cutting-edge of cutting technology and tool industry is largely due to the fact that the use of tools by companies is stuck on old traditional concepts, that is, the use of cheap tools to control costs, rather than Use high-efficiency tools to reduce costs by increasing processing efficiency.
If CNC machine tools, machining centers and other advanced cutting machine tools are equipped with corresponding efficient tools, there will be no market for low-grade tools and counterfeit products. The Chinese processing industry will make a big step forward. Although the tooling cost in modern processing only accounts for 3% to 4% of the manufacturing cost, it has a great influence on the total cost, the processing efficiency is increased by 20%, the processing cost can be reduced by 15%, and although the use of cheap cutting tools reduces the price by 20%, The processing cost is only reduced by 0.5%; the tool life is extended by 1 time and the processing cost can only be reduced by 1.5%. So more and more people realize that increasing tool input for high-speed machining is the most effective means to increase efficiency and reduce costs. This is a leap in the cutting concept in recent years. I hope this idea will become a conscious action of the company.
(2) The concept of production and management The harm caused by conservative and unconcerned conservative concepts in the development of modern and efficient cutting tools in our country far exceeds the impact of technological backwardness. From the development of traditional standard tools to modern, efficient cutting tools, the Chinese tool industry has undergone a revolutionary process that is reborn and full of difficulties and hardships. This process of change has caused some companies to back down, not to meet difficulties, but to stand still or even to regress. In this regard, it should be recognized that change is the need of the times; if it is unchanged, it will retreat or die. China's manufacturing industry is developing at an alarming rate. It is only taking auto manufacturing as an example: It took 36 years from 1956 to 1992 to develop to 1 million vehicles, and it took only 4 years from 1992 to 1996. The production of 1.5 million vehicles has become a geometric progression in the future. In 2008, it exceeded 10 million vehicles. China has become a global leader in automobile production, and the automotive industry is a leading industry. Its rapid development has driven the passive development of related industries. A huge modern manufacturing system has risen in China. Therefore, regardless of the survival space of China's tool industry or the overall needs of China's entire manufacturing industry to improve competitiveness, cutting tool companies accelerate structural adjustment and promote efficient tools. The development has been unavoidable. The result of stagnation and stereotypes is the collapse. Only by changing the theory of production and operation, and liberating from the traditional standard tool cages, manufacturing high-efficiency cutting tools that meet market demands and marketable is the only way to go. Pay Attention to Material Selection and Quality Improvement In machining, cutting is the most basic and reliable method of precision machining.
In the 21st century, the competition in the machinery manufacturing industry is essentially the competition of precision high-speed cutting. This competition is all-round. At present, with the adoption of new high-rigidity integrated casting machines, high-speed arithmetical numerical control systems, and spindle dynamic balancing, as well as the continuous development of tool materials, modern cutting technologies are moving in the direction of high-speed, high-precision, and powerful cutting. The performance, quality, and reliability of tool materials directly affect the manufacturing efficiency of millions of expensive CNC machine tools in China's manufacturing industry, and the quality of processing. It also directly affects the level of production technology and the economy of the entire machinery manufacturing industry. The level of benefit. "The dividends of enterprises are on the cutting edge" vividly represents the status and role of the tool in the enterprise. The tool material is the basis of the tool industry, and the development of tool materials plays a decisive role in the improvement of the cutting performance of the tool. Without a good tool material, where does a good tool come from? Where does efficient cutting come from? High-speed steel was introduced in 1900, which increased the cutting speed by 3 times compared with the original alloy steel cutting tools. The carbide cutting tools promoted in the middle of the 20th century increased the cutting speed by 2-3 times compared with high-speed steels; Ceramic and other super-hard material tools, but also to increase the cutting speed several times. The current tool materials mainly include high-speed steel, carbide and superhard materials.
(1) High speed tool steel GB/T9943-2008 "High Speed ​​Tool Steel" divides high speed steel into three grades: low alloy high speed steel (HSS-L), common high speed steel (HSS), high performance high speed steel (HSS-E) ). The so-called low-alloy high-speed steel is a high-speed steel with a tungsten equivalent (W+2Mo) of less than 12% but ≥ 7%. After appropriate heat treatment of this steel, the hardness can be ≥63HRC. It plays an important role in the low-speed cutting tools such as rolling twist drills and machine taps. However, many domestic tool experts do not agree that they do not meet the high-speed steel Performance requirements, suspected of being fake and inferior, have a bad international reputation and should be expelled from high-speed steel. In fact, since the HSS-L was introduced in China in the 1980s, all over the country, especially in Jiangsu and Zhejiang, the use of alloy steels to impersonate low-alloy high-speed steel, knowing that it is not a high-speed steel, is reputed in the commodity. The "HSS" on the landmark is really "No silver here and here and there." HSS-E is based on the HSS appropriate increase in Co, V, Al and other elements, and the corresponding increase in C, in order to increase its hardness and red hardness. Although the price of materials is expensive, it highlights the energy when cutting difficult-to-machine materials. Due to the rapid development of CNC machine tools, machining centers and difficult-to-machine materials, the application of HSS-E will gradually increase. The mechanical properties of powdered high-speed steel are significantly higher than that of smelting high-speed steel. The strength can be increased by 20% to 30%, and the toughness can be increased by 1.5 to 2 times. And the safety and reliability are strong. The tool life is several times or even dozens of times that of HSS steel tools. It has been widely used abroad, but it has rarely been adopted in China.
(2) Cemented carbide high-speed steel dominates tool materials for more than 100 years. Due to the rapid development of high-speed cutting, dry cutting, and hard cutting, carbide has become the new dominant tool material. In recent years, due to the development and utilization of rare earth metal-added hard alloys, application of nanotechnology, and ultra-fine particle cemented carbide and superhard coating technologies for improving strength and toughness, the high-efficiency cutting performance of cemented carbides has been significantly improved. Widening the application of cemented carbide, now highly efficient cutting tools, is basically dominated by carbide.
(3) Superhard tool materials These materials mainly refer to ceramics, cubic boron nitride, and diamond. They have high hardness and wear resistance, so they can improve cutting efficiency. The application range in the manufacturing industry has gradually expanded in recent years. Superhard cutting tools and their materials have production bases and suppliers in China. The key question is whether users are sincerely using them. In the mold processing industry, super-hard tools have played an important role, and it is convinced that such tool materials will have a very broad application prospect. Good tool materials must have good heat treatment for support. Such as the application of Ace High Speed ​​Steel M42. At present, there are two misunderstandings on the use of M42 steel: First, the blind pursuit of high hardness; Second, the formulation of the heat treatment process. Superhard high-speed steel does not have to be superhard. M42 steel can reach 68~70HRC through appropriate heat treatment. Such high hardness is not suitable for most tools. Tool life has always been based on the hardness of heroes, we pursue high hardness, but not only high hardness, we must To meet toughness, we strive for high hardness. Although the same brand of high-speed steel production of different tools, heat treatment process should be not used, that is, should be personalized heat treatment process, the formula of heat treatment process has fallen behind. Surface hardening techniques such as PVD and CVD have achieved major developments in cutting tools, and even super hard tools such as hard alloys have been added.
However, it should be remembered that no matter how good the coating has to be supported by good pre-treatments, such as high-speed steel tools with low hardness or over-heating, the coating will not have good results. Therefore, if you want to strengthen the surface, the foundation must be firmly secured. Technological innovation and catching up with the country to "enhance efficiency and reduce costs" are the core of global manufacturing competition. Who does not want to make money? With rising prices of raw materials and energy, workers' wages and related expenses are rising, and the sales price of products can never keep up with the increase in costs. All tool industries face the test of survival and development. Therefore, we must think of ways to improve labor productivity and take the road to technological innovation. The long-term economic growth of developed countries depends mainly on technological innovation. According to statistics, in the global investment in science and technology development, the Western seven countries accounted for 90%, of which the input of enterprises accounted for more than 70%, so 80% of the global intellectual property rights are owned by seven Western countries and multinational companies. Developed countries rely on this advantage to monopolize capital in the high-end technology of the industrial chain.
Modern tool companies bear the heavy responsibility of improving the labor productivity of the manufacturing industry. Therefore, developed countries have invested heavily in the development of new materials for cutting tools, new coatings, new technologies, new processes, and tool-specific digital manufacturing technologies. They have developed generations of high-efficiency tools and have firmly occupied the international tool. In the high-end market, there are also dozens of foreign tool makers operating their cutting-edge tools in China. China's Shanggong, Chengquan, Haliang, Hanjiang, Hengfeng, Zhuzhou Diamond, Xiamen Golden Heron and other well-known tool companies, developed the root slot milling cutter, hard alloy gear hob, Christmas tree milling cutter, octagonal milling cutter , Hard alloy modular knife, wave-edge end mills, non-standard slotting knives, as well as HSK tool handles for high-speed cutting tools, double end face handles are quite lethal. Although many domestic enterprises have strong technological innovation capabilities, there are still large gaps compared with well-known foreign companies. Therefore, we have increased our efforts to develop cutting tools as a long-term strategic task. We have taken a solid step in the manufacture of complex and efficient tools, and have made our due contributions to catching up with the power of the world. Strengthen services to stabilize the market For the tool industry, only high-quality branded products are far from enough, and it is more important to provide customers with comprehensive metal cutting solutions.
Toolmakers should move from simply supplying standard tool products to producing strategic, personalized and advanced cutting tools and providing services. Speaking of services, people naturally think of services such as after-sales services and technical services. However, the service I talk about here is an innovative concept that relates to the business model of the company. Simply put, a product-based company processes enamel materials into tools to earn processing fees; a development-oriented enterprise sells both tools and technology; service-oriented companies not only sell tools, but also provide technical support and other services. The practice of some foreign tool makers is worth learning from. For example, on April 1 this year, Sandvik Coromant Greater China Chengdu Training Center officially opened its doors and invited well-known cutter experts from home and abroad to teach. Since the establishment of the Shanghai Efficiency Center in 2004, Sandvik Coromant has successively opened training centers in Tianjin, Guangzhou, Xi'an and other places, and established an application center in Shanghai. This series of measures can not only provide users with better training and services, but also communicate and share experiences with industry colleagues, and jointly promote the rapid development of the tool industry. In today's increasingly refined manufacturing industry, cutting tool companies need to extend service, increase service items, and improve service levels. This is a key move to increase the competitiveness of enterprises. "There is a sense that the wine is not afraid of the deep alley", but it is not comprehensive. The power of advertising and advertising cannot be underestimated. In the era of planned economy, under the influence of “small and complete†and “large and completeâ€, for the tool industry-related companies, they have their own tool manufacturing workshops and even branch factories, in addition to purchasing some standard tools in the market. The other tools were solved by themselves, and it was deemed that there was no need to request service requirements from the tool industry. Today is not the same, more and more manufacturing industry, not only removed the tool shop, and even the tool grinding department is also gone, and even tool engineers, craftsmen are all downsizing, its purpose is to highlight the main business, Accelerating development is a major step forward in the manufacturing industry's advancing with the times. However, the tools and processes within the manufacturing industry have to be managed. Who will fill this vacancy? Definitely a tool manufacturing industry, that is, a specialized division of labor. This division of labor requires the tool companies to dare to reform and innovate, to cross the old tools of traditional tools and after-sales service, to show the new style of modern tool companies. Under the framework of modern manufacturing, the future development path of tool companies can only be achieved through upgrading their ability to provide full-service for the manufacturing industry. It is thus possible to become a stable partner in the industrial chain of the manufacturing sector, and thus obtain stable and reliable market share.
Middle Duty Caster Co., Ltd. , http://www.nbcasters.com