Various performance indicators of raw materials for gaskets
A metal gasket material
1. Carbon steel:
The recommended maximum operating temperature does not exceed 538 ° C, especially when the medium is oxidizing. High-quality thin carbon steel sheets are not suitable for use in equipment for the production of inorganic acid, neutral or acidic salt solutions. If carbon steel is stressed, the equipment accident rate under hot water conditions is very high. Carbon steel gaskets are commonly used for high concentrations of acids and many alkaline solutions. The Brinell hardness is about 120.
2. 304 stainless steel
18-8 (chromium 18-20%, nickel 8-10%), the recommended maximum operating temperature does not exceed 760 °C. In the temperature range of -196~538 °C, stress corrosion and grain boundary corrosion are prone to occur. Brinell hardness of 160.
3. 304L stainless steel
The carbon content does not exceed 0.03%. The recommended maximum operating temperature does not exceed 760 °C. Corrosion resistance is similar to 304 stainless steel. The low carbon content reduces the precipitation of carbon from the crystal lattice, and the resistance to intergranular corrosion is higher than that of 304 stainless steel. The Brinell hardness is about 140.
4. 316 stainless steel
18-12 (chromium 18%, nickel 12%), adding about 2% molybdenum in 304 stainless steel, when the temperature increases its strength and corrosion resistance. It has higher creep resistance than other common stainless steels when the temperature is increased. The recommended maximum operating temperature does not exceed 760 °C. The Brinell hardness is about 160.
5. 316L stainless steel
The recommended maximum continuous operating temperature does not exceed 760 ° C ~ 815 ° C. The carbon content does not exceed the resistance to stress and grain boundary corrosion of 316 stainless steel. The Brinell hardness is about 140.
6. 20 alloy
45% iron, 24% nickel, 20% chromium and a small amount of molybdenum and copper. The recommended maximum operating temperature does not exceed 760 ° C ~ 815 ° C. It is especially suitable for the manufacture of equipment resistant to sulfuric acid corrosion with a Brinell hardness of approximately 160.
7. aluminum
Aluminum (content not less than 99%). Aluminum has excellent corrosion resistance and processing properties and is suitable for the manufacture of double-clamp gaskets. The Brinell hardness is about 35. The recommended maximum continuous operating temperature does not exceed 426 °C.
8. Copper
The composition of copper is close to pure copper, which contains traces of silver to increase its continuous operating temperature. The recommended maximum continuous operating temperature does not exceed 260 °C. The Brinell hardness is about 80.
9. brass
(66% copper, 34% zinc), it has good corrosion resistance under most working conditions, but it is not suitable for acetic acid, ammonia, salt and acetylene. The recommended maximum continuous operating temperature does not exceed 260 °C. The Brinell hardness is about 58.
10. Hastelloy B-2
(26-30% molybdenum, 62% nickel and 4-6% iron). The recommended maximum operating temperature does not exceed 1093 °C. It has excellent heat resistance and hydrochloric acid corrosion performance. It also has excellent resistance to wet hydrogen chloride gas corrosion, sulfuric acid, phosphoric acid and reducing salt solution corrosion. It has high strength under high temperature conditions. The Brinell hardness is about 230.
11. Hastelloy C-276
(16-18% molybdenum, 13-17.5% chromium, 3.7-5.3% tungsten, 4.5-7% iron, the balance are all nickel). The recommended maximum operating temperature does not exceed 1093 °C. Has excellent corrosion resistance. It has excellent corrosion resistance for various attempts of cold nitric acid or boiling nitric acid with a concentration of 70%, good resistance to hydrochloric acid and sulfuric acid corrosion and excellent stress corrosion resistance. The Brinell hardness is about 210.
12. Inconel 600
Nickel based alloy (77% nickel, 15% chromium and 7% iron). The recommended maximum operating temperature does not exceed 1093 °C. It has high strength under high temperature conditions and is usually used in equipment that needs to solve stress corrosion problems. Excellent low processing performance at low temperatures. The Brinell hardness is about 150.
13. Monel 400
(30% copper, 63% nickel) The maximum continuous operating temperature is recommended to not exceed 815 °C. In addition to strong oxidizing acids, it has excellent corrosion resistance for most acids and bases. Stress corrosion cracking is likely to occur in hydrofluoric acid, mercuric chloride, and mercury media, and thus, it is not suitable for the above medium. A device widely used in the manufacture of hydrofluoric acid. The Brinell hardness is about 120.
14. titanium
The recommended maximum operating temperature does not exceed 1093 °C. Excellent corrosion resistance at high temperatures. It is well known that it is resistant to chloride ions and has excellent resistance to nitric acid corrosion over a wide range of temperatures and concentrations. Titanium is used in most alkaline solutions and is suitable for use in oxidizing conditions. The Brinell hardness is about 216.
2. Non-metallic gasket material
1. Natural rubber NR
It has good corrosion resistance to weak acids and bases, salt and chloride solutions, and poor corrosion resistance to oils and solvents. It is not recommended for ozone media. Recommended operating temperature -57 ° C ~ 93 ° C.
2. Neoprene CR
Neoprene is a synthetic rubber that is suitable for corrosion of acids, bases and salt solutions that are resistant to moderate corrosion. Good corrosion resistance to commercial oils and fuels. However, the corrosion resistance of strong oxidizing acids, aromatic hydrocarbons and chlorinated hydrocarbons is poor. Recommended operating temperature -51 ° C ~ 121 ° C.
3. fluororubber
Good corrosion resistance to oils, fuels, chloride solutions, aromatic hydrocarbons and aliphatic hydrocarbons and strong acids, but not applicable to amines, lipids, ketones and steam, recommended operating temperature -40 ° C ~ 232 ° C .
4. Chlorosulfonated polyethylene synthetic rubber
It has good corrosion resistance to acid, alkali and salt solutions, and is not affected by climate, light, ozone, commercial fuels such as diesel and kerosene. It does not apply to aromatic hydrocarbons, chlorinated hydrocarbons, chromic acid and nitric acid. Recommended operating temperature -45 ° C ~ 135 ° C.
5. Silicone Rubber
Good corrosion resistance to hot air. Silicone rubber is not affected by sunlight and ozone. However, Wang is suitable for use in steam, ketones, aromatic hydrocarbons and aliphatic hydrocarbons.
6. Ethylene propylene rubber
Good corrosion resistance to strong acids, strong bases, salts and chloride solutions. It does not apply to oils, solvents, aromatic hydrocarbons and hydrocarbons. Recommended operating temperature -57 ° C ~ 176.
7. Graphite This material contains no resin or inorganic all-graphite material and can be classified into a metal with or without a metal element. The material can be bonded to make pipe gaskets over 600 mm in diameter. It has excellent corrosion resistance to many acids, bases, salts and organic compounds and heat transfer solutions, even high temperature solutions. It does not melt, but it will sublimate beyond 3316 °C. In high temperature conditions, the use of this material in a strong oxidizing medium should be cautious. In addition to being used for gaskets, this material can also be used to make non-metallic wound tapes in fillers and wound gaskets.
8. Ceramic fiber
The ceramic fiber formed on the strip is an excellent gasket material suitable for high temperature and low pressure working conditions and light flange conditions. The recommended working temperature is 1093 ° C, and the non-metallic winding tape in the wound gasket can be made.
9. PTFE
It combines the advantages of most plastic gasket materials, including temperature resistance from -95 ° C to 232 ° C. In addition to free fluorine and alkali metals, it has excellent corrosion resistance to chemicals, solvents, hydroxides and acids. PTFE material can be charged
High water-based packing range: mainly emulsion, water or oil. Applicable to oilfield high pressure mud pump, coal mine underground hydraulic support, emulsion and so on. The rubber ring used in the original cloth has a short life span and frequent replacement, and the labor intensity is large, which not only delays the production, but also affects the economic benefits and seriously pollutes the environment. After using this product, the lifespan is greatly extended, and it is less than a few months and more than half a year.
Features: This filler does not contaminate the product. Less maintenance, easy to install, no wear on the sealing parts.
Technical Parameters:
Temperature: -20 ° C ~ +150 ° C
Pressure: 35MPa
Chemical resistance: PH value 4-12
Expanded graphite packing
The expanded graphite packing is woven by a flexible graphite wire. It has the advantages of good self-lubricity and thermal conductivity, small friction coefficient, strong versatility, good flexibility, high strength and protection for the shaft. According to different requirements, it can be reinforced with carbon fiber, glass fiber and other materials.
Expanded graphite packing is a universal packing, recommended for use in petroleum equipment, power plants, chemicals, steel mills, etc. Suitable for hot water, high temperature, high pressure, steam, heat exchange medium, ammonia, hydrogen, organic solvents, hydrocarbons, cryogenic liquids and other media.
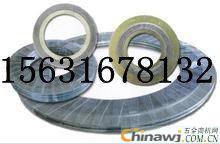
Metal sheet & tube Laser Cutting Machine available for metal plate and tube cutting in various materials such as stainless steel, carbon steel, alloy steel, spring steel, copper, aluminum, gold, sliver, titanium etc.
Metal sheet & tube laser Cutting Machine advantage:
1. Auto - focus
Applicable to various focal lengths, which are controlled by machine tool control system. Focal point will be automatically adjusted in cutting process to achieve the best cutting effect of different thicknesses sheets metal.
2. Free
Focal length is controlled by operating system. We don`t need to do manual regulation, which effectively avoids errors or faults caused by manual operation.
3. Fast
Auto focus would automatically adjust the most appropriate focal points in the process of punching and cutting, which greatly improves cutting speed;
4. Accuracy
Metal sheet & tube laser cutting machine with increasing perforation focus length, separately setting perforation focal length and cutting focal length, enhance cutting accuracy.
Metal Sheet & Tube Laser Cutting Machine
Laser Tube Cutting Machine,Metal Laser Cutting Machine,Metal Laser Cutter,Laser Cutter
Jinan Huaxia Machinery Equipment CO.,Ltd , http://www.cnformingmachine.com